Maximizing Efficiency and Performance with Central Lubrication Systems
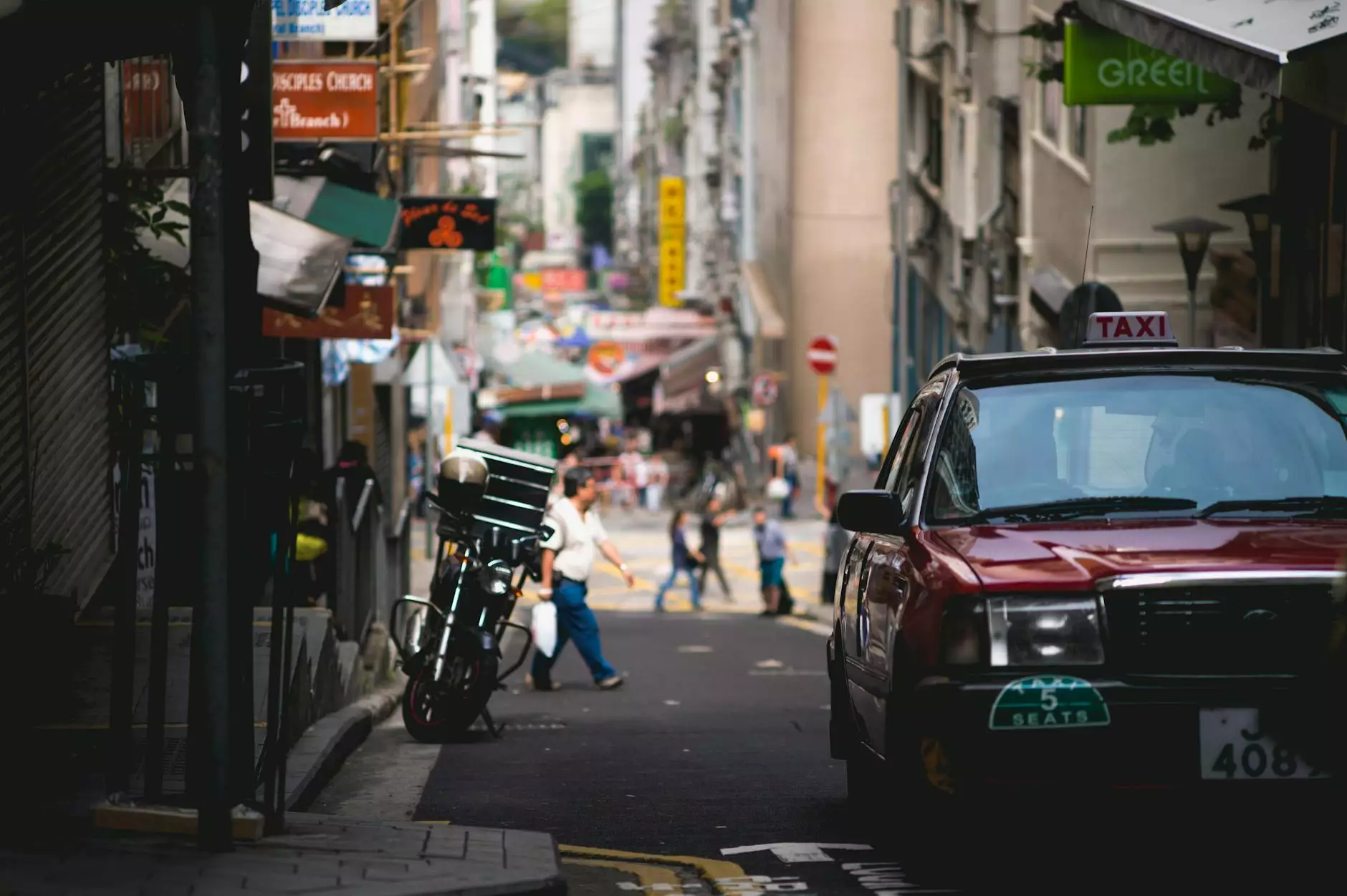
Introduction
In today's industrial landscape, where efficiency and productivity are paramount, businesses are constantly seeking innovative solutions to streamline their operations. One crucial aspect often overlooked is the proper maintenance and lubrication of industrial machinery. This is where a central lubrication system comes into play – a specialized mechanism designed to ensure optimal performance and longevity of equipment.
What is a Central Lubrication System?
A central lubrication system, also known as a centralized lubrication system or an automated lubrication system, is a sophisticated mechanism that automates the lubrication process for industrial machinery. It eliminates the need for manual lubrication, providing a consistent supply of lubricant to all the necessary components, ensuring smooth operation and reducing downtime caused by inadequate lubrication.
How Does a Central Lubrication System Work?
The central lubrication system is comprised of several key components, all working together to achieve optimum lubrication efficiency. One essential element is the central lubrication pump, responsible for pumping the lubricant throughout the system. The pump is connected to a reservoir containing the lubricant, which is dispensed through distribution lines and fittings to various lubrication points on the machinery.
Benefits of Central Lubrication Systems
The adoption of a central lubrication system offers numerous advantages, enhancing both productivity and cost-effectiveness:
1. Increased Equipment Lifespan
Adequate and consistent lubrication is crucial in prolonging the lifespan of industrial machinery. Central lubrication systems ensure that all lubrication points receive the required amount of lubricant, reducing friction and wear on critical components. By reducing the strain on equipment, businesses can avoid premature failures, costly repairs, and expensive downtime.
2. Enhanced Operational Efficiency
With a central lubrication system in place, manual lubrication tasks become a thing of the past. This allows operators and maintenance personnel to focus on other important tasks, improving overall operational efficiency. Additionally, the automated system ensures that the right amount of lubricant is supplied at the right time, eliminating the risk of either under or over-lubrication.
3. Time and Labor Savings
By eliminating the need for manual lubrication, businesses can save substantial amounts of time and reduce labor costs. With a central lubrication system, lubrication points are easily accessible, enabling quick and efficient maintenance procedures. Workers can now focus on more critical tasks, allowing for better resource allocation and increased productivity.
4. Improved Safety and Environmental Standards
Central lubrication systems can help businesses meet safety and environmental regulations. By controlling the lubricant supply and reducing the risk of leaks or spills, these systems minimize the potential hazards associated with manual lubrication methods. Furthermore, automated systems often use environmentally friendly lubricants, contributing to a healthier work environment and reducing the company's ecological footprint.
Conclusion
As businesses strive for efficiency, adopting a central lubrication system has become a necessity rather than a luxury. These systems provide the critical lubrication needed for industrial machinery, ensuring optimal performance, extended lifespan, and increased productivity. By eliminating the inconsistencies and challenges of manual lubrication tasks, companies can maximize their operational efficiency, reduce maintenance costs, and achieve a competitive edge in today's highly demanding market.