Understanding the Importance of Wire Tagging Machines in Modern Packaging
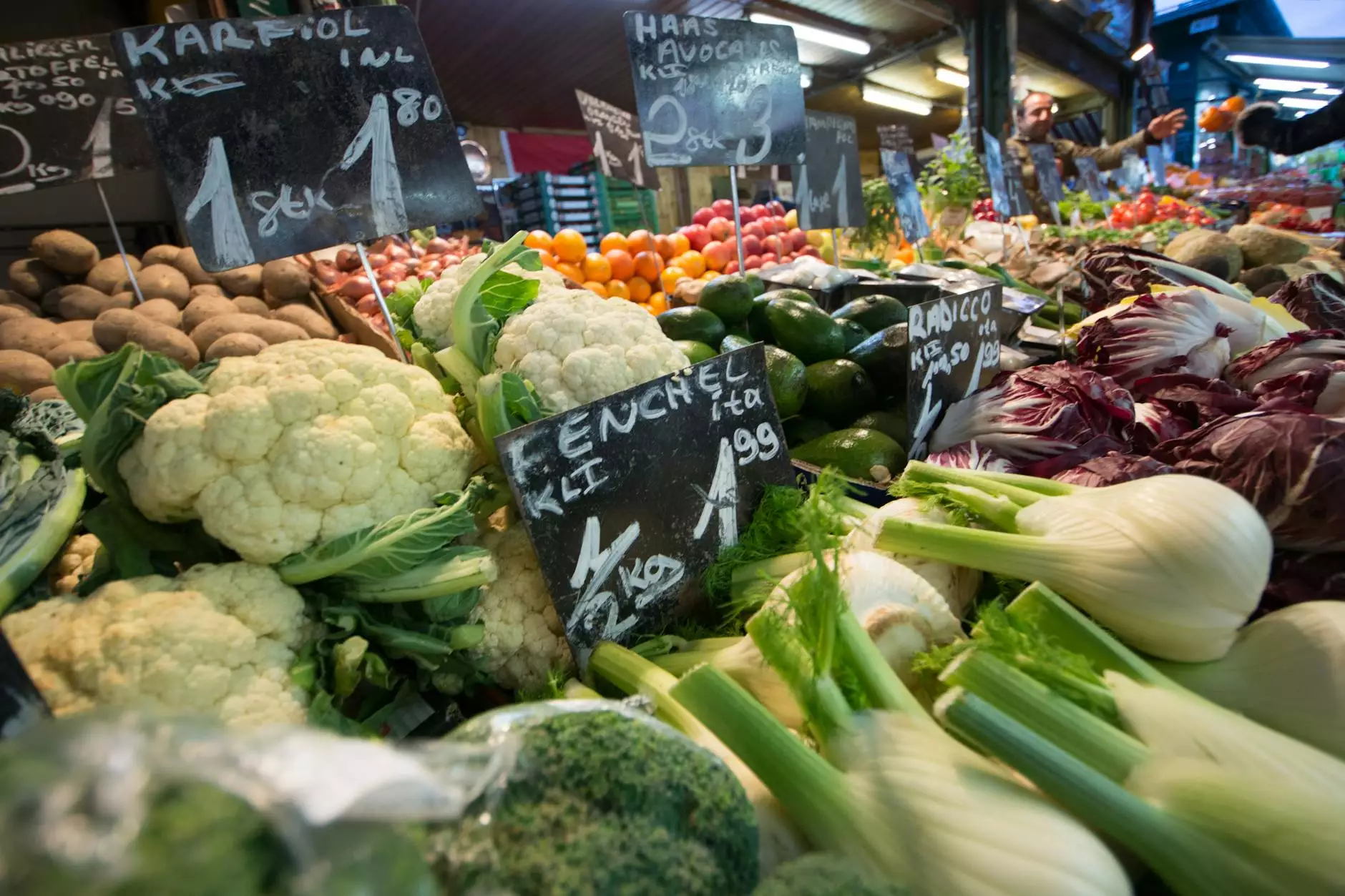
The packaging industry is rapidly evolving, becoming more efficient and cost-effective due to advanced technologies and machinery. One of these groundbreaking innovations is the wire tagging machine. This machinery plays a critical role in ensuring that products are identified, traced, and managed effectively throughout the supply chain. In this article, we will delve into the definition, benefits, types, applications, and future trends of wire tagging machines, focusing on their significance in the packaging equipment sector.
What is a Wire Tagging Machine?
A wire tagging machine is an automated device used to fasten identification tags to wires and cables. These machines utilize a variety of tagging methods, including adhesive labels, string tags, or plastic tags, to create a reliable identification system. They are beneficial in various industries, including electronics, manufacturing, and logistics, where precise product identification is essential.
The Benefits of Using Wire Tagging Machines
Wire tagging machines bring numerous advantages to businesses within the packaging industry. Here are some key benefits:
- Enhanced Efficiency: Automation reduces manual labor and speeds up the tagging process, allowing businesses to handle larger production volumes.
- Improved Accuracy: Machines ensure that tags are applied correctly, minimizing errors that can occur with manual labeling.
- Cost-Effective: By streamlining operations, wire tagging machines help lower labor costs and reduce the risk of product loss or misidentifier, which can be quite costly.
- Consistency: They provide uniformity in tagging, ensuring all products are labeled following industry standards.
- Traceability: By employing coded tags, businesses can easily track products throughout the supply chain, enhancing inventory management and accountability.
Types of Wire Tagging Machines
When considering a wire tagging machine, it is essential to understand the different types available, as each serves unique functions and applications. Here’s a look at some of the most common types:
1. Manual Wire Tagging Machines
These machines require operators to manually position the wires and attach the tags. While less efficient than automated systems, they are more affordable and suitable for low-volume operations.
2. Semi-Automatic Wire Tagging Machines
Semi-automatic machines combine manual and automatic processes. Operators load and position the items, but the machine performs the tagging automatically. These machines offer a good balance between cost and efficiency.
3. Fully Automatic Wire Tagging Machines
These machines fully automate the tagging process. They are equipped with advanced features such as sensors and conveyor belts, making them ideal for high-volume production environments.
4. Customizable Wire Tagging Machines
Many manufacturers offer customizable machines tailored to specific business needs. These can integrate various features, such as different tag sizes, printing options, and software compatibility.
Applications of Wire Tagging Machines
Wire tagging machines have a wide range of applications across various sectors. Here are some notable examples:
1. Electronics Industry
In the electronics sector, products such as wires, connectors, and circuit boards require precise tagging for quality control and traceability. Wire tagging machines ensure that each component is accurately labeled.
2. Manufacturing
Manufacturers use wire tagging for identifying machinery parts, raw materials, and finished goods. Proper tagging reduces mismanagement and enhances efficiency in the production cycle.
3. Logistics and Warehousing
Effective logistics management relies heavily on accurate tagging. Companies utilize wire tagging machines to maintain proper inventory control and facilitate easy tracking of items throughout the supply chain.
4. Telecommunications
Telecommunication companies rely on tagging for their fiber optic and copper cables. Tagging aids in identifying specific cables during installation and maintenance.
Choosing the Right Wire Tagging Machine
When looking for the right wire tagging machine, consider the following factors:
- Production Volume: Assess your production requirements. High-volume operations may benefit from fully automatic machines, while smaller businesses might find manual or semi-automatic solutions adequate.
- Tagging Method: Determine what type of tags you need—plastic, paper, or metal—and choose machines that can handle those materials.
- Integration: Ensure the machine can integrate seamlessly with your existing systems and processes for optimal efficiency.
- Budget: Establish a budget and consider both the initial and long-term costs of ownership.
- Support and Maintenance: Look for manufacturers that provide ongoing support and maintenance to ensure your machinery remains operational.
Future Trends in Wire Tagging Machines
The future of wire tagging machines is bright, driven by technological advancements and evolving industry needs. Here are some emerging trends to watch:
1. Smart Technology Integration
With the rise of Industry 4.0, smart technology is making its way into packaging machinery. Machines are incorporating IoT features for real-time tracking, data analysis, and remote monitoring.
2. Increased Customization
As companies seek to differentiate their products, the demand for customizable tagging solutions is growing. Manufacturers are responding by developing machines that allow for greater flexibility in tag design and application.
3. Eco-Friendly Tagging Solutions
With sustainability becoming more crucial, there is a push for eco-friendly tagging materials and processes. Companies are looking for low-waste tagging solutions that minimize their environmental impact.
4. Enhanced User Interface and Experience
Modern machines are evolving to include user-friendly interfaces that simplify operation and training. Touchscreen controls and automated setup processes are becoming standard features.
Conclusion
In conclusion, the wire tagging machine is an indispensable asset in the packaging industry. Its efficiency, accuracy, and versatility greatly enhance productivity and product traceability. By understanding the various types, benefits, applications, and future trends of these machines, businesses can make informed decisions that align with their operational goals and market demands. As we move forward, investing in advanced tagging solutions will undoubtedly play a critical role in maintaining competitive advantages in the ever-evolving packaging landscape.
For more information on high-quality packaging equipment and innovative wire tagging solutions, visit shineben.com.